Dedicated sublimation printers produce vibrant and long-lasting prints that are machine washable. They also do not need a complex color management system like you’d find in regular inkjet printers.
Before starting the setup process, you’ll need to fill up the tanks with the corresponding ink color using either a syringe or a bottle (they are color-coded). Next, set up your heat presses and prepare your transfer paper. Click the Epson Dye Sublimation Printer to learn more.
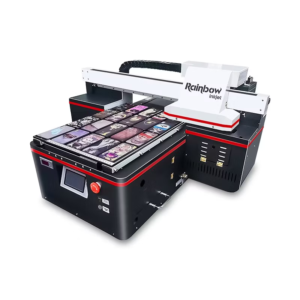
The Epson dye sublimation printer is a fast, high-quality printing machine that can print a large number of garments in a short period of time. It is an excellent choice for small and medium businesses that specialize in producing custom apparel, signs, banners, or novelty items like coffee mugs and coasters.
It is easy to use and offers a variety of features that make it ideal for beginners and experts alike. The printer also passes rigorous chemical testing, making it safe for use on children’s clothing and other textiles.
The Epson F170 is a small, entry-level dye sublimation printer that can be used for a wide range of applications. Its high-resolution output and vibrant colors make it an excellent choice for printing onto polyester and polymer-coated substrates. The printer is also a great choice for home and business users who want to print their own clothes or other items using their own designs.
This Epson dye sublimation printer comes with a set of full-size ink tanks and is sold at a reasonable price. However, it is important to note that the first set of ink will be used to charge the print heads. This will make it less expensive for the first few prints but will increase the cost of replacement inks over time.
Another good option for a small business is the Epson EcoTank series. These printers are designed for high-volume printing and have a low cost per print. The ET-2400, for example, has a max print resolution of 5760 x 1440 dpi and can handle a large amount of media. Its small footprint makes it an excellent choice for those with limited space.
The SureColor F6470H is a high-performance dye-sublimation transfer printer that delivers professional-grade, 6-color output at speeds up to 400 ft2/hr1. This is perfect for photographic panels, promotional products, apparel, soft signage, and more. It uses a 1.33″ PrecisionCore MicroTFP printhead with Nozzle Verification Technology and an integrated ink pack system with 1.6-liter UltraChrome DS Ink packs to deliver astounding image quality with rich color saturation and contrast.
Printing Resolution
The printing resolution of a dye sublimation printer is one of the most important factors that determines print quality. Higher resolutions result in sharper images and superior printing outcomes. However, it’s not as simple as choosing a high resolution to achieve better print quality; a variety of other factors play an equally significant role in ensuring that prints are crisp and detailed. For example, the material’s surface texture and ink absorption capabilities have a direct impact on the final print quality. Moreover, a good design must be carefully prepared and uploaded to the printer for optimal results.
Blurry or pixelated images are a common occurrence in sublimation printing, but can be avoided by ensuring that the digital image resolution matches the print resolution. Choosing a suitable coating for the material’s surface is also necessary to prevent ink dots from blending together, resulting in blurred image outlines. Regular printer calibration is also essential to avoid misalignment in the timing of ink droplet ejection and paper advancement, which can lead to image fuzziness.
Another factor that contributes to the print quality of a dye sublimation printer is the print size and print area specifications. It’s important to choose a file format and color profile that are appropriate for the print size and area you’re creating. For instance, raster file formats are ideal for photographs and scanned artwork, while vector files are a great choice for designs that require crisp lines. In addition, mastering the manipulation of print size and scaling is an essential skill to obtain superior sublimation results.
The SureColor F6470PE is a 64-inch dye-sublimation transfer printer that delivers professional-quality, 6-color output at a speed of up to 1,169ft2/hr1. It features dual PrecisionCore MicroTFP printheads with Nozzle Verification Technology and UltraChrome DS ink packs for astounding image quality. This dye-sublimation printer is perfect for producing high-quality apparel, soft signage and photo panels. Moreover, it offers a space-saving design for enhanced workshop usability and a 1.6-liter ink pack system for efficient high-volume printing. It’s an ideal solution for any busy production environment. This machine requires a heat press to complete the process.
Ink Consumption
When working with dye sublimation printers, it is essential to understand the ink consumption. While these printers are capable of high print speeds, the ink can quickly deplete if not managed correctly. It is recommended to monitor the ink levels and replace the cartridges before running out of ink. This will help to avoid any costly downtime for your business and ensure that the highest quality prints are produced.
The Epson Dye Sublimation Printer is a wide-format machine that can print designs on fabric. It uses heat and pressure to transfer the dye ink to the material, resulting in a vibrant color. These printers can be used for a variety of applications, including apparel, promotional products, and soft signage. The printer is also easy to use and provides high-quality results.
Unlike traditional inkjet printers, these dye sublimation printers utilize an industrial-grade print head that produces accurate and consistent results. The print heads feature MicroPiezo technology, which offers quick vibration and flexion to disperse the ink on the media. This ensures that the ink is applied evenly across the surface of the substrate. Additionally, the print heads are designed to resist clogs and provide smoother printing for high-volume jobs.
This printer is available in a range of sizes and colors, making it ideal for a variety of industries. It is easy to operate and offers a low cost of ownership. Moreover, the machine features six 4.7” PrecisionCore printheads and a high-capacity ink pack system to maximize productivity. This allows you to produce stunning, high-quality images at a fast rate of up to 400 ft2/hr1.
To get the most out of your Epson dye sublimation printer, follow these tips:
Use Epson’s genuine ink and transfer paper: Third-party inks may seem cheaper, but they can lead to poor print quality and clogged print heads. Stick to Epson’s dye sublimation inks and transfer papers that are specifically designed for your Epson model, as they will provide the best results.
Perform regular color checks: For high-volume projects, it is important to test your prints regularly to ensure that they are accurate. This will allow you to catch any problems with your color management settings, which can cause a shift in hues and prevent your prints from meeting your customer’s expectations.
Warranty
A dedicated dye-sublimation printer is ideal for businesses and serious hobbyists who need a high-performance machine that can handle large volume printing jobs. The Epson ET-15000 features advanced printing technology, automatic duplexing, and wide format capabilities to deliver exceptional print quality. It also offers a range of connectivity options and user-friendly setup and maintenance. However, it is not the fastest sublimation printer in the market, and its slower print speed may not be suitable for demanding applications.
Unlike inkjet printers, which require the use of special cartridges, dye-sublimation printers use unique print heads that are designed to work with sublimation inks. Using different inks in these printers can damage the print head, and if left unchecked could result in irreparable damage to the entire printer. The ET-15000 is one of the few models on the market that offers a warranty for its print heads, which provides peace of mind for users who plan to use the printer for a long time.
The ET-15000 has a large display screen that allows you to monitor and manage your job progress in real time. It is easy to use and can be set up to run on your network or directly from your computer. It is designed with an intuitive interface and a color touch panel for simplified operation. Its built-in power supply eliminates the need for external devices and makes it easier to maintain.
While the ET-15000 is a great choice for larger businesses, smaller ones may want to consider other models with a more compact footprint. For example, the Epson SureColor F170 is a 44-inch desktop printer that is designed to print on rigid and textile substrates. It uses the PrecisionCore MicroTFP printhead to create high-resolution images with minimal nozzle clogging. It is equipped with 1.6-liter UltraChrome DS ink packs that provide stunning image quality.
The SureColor F170 is a dedicated sublimation printer, meaning it’s made specifically for sublimation and doesn’t void the Epson warranty like converted EcoTank printers do. It comes with everything you need to start sublimating right out of the box, including a 21ml starter set of ink and Sublisure A4 paper. The printer is also available with extended on-site service plans, which can be purchased for a low price and are redeemable with loyalty points.